Superior CIP Technology
COLD ISOSTATIC PRESSES
A Leader in CIP Innovation & Dependability
For more than 30 years American Isostatic Presses has led the industry in developing cutting edge cold isostatic pressing (CIP) technology. AIP has never had a failure of any pressure system we’ve installed. AIP research systems are extremely simple and economical, allowing organizations the ability to own one or more systems in house. AIP Cold Isostatic Presses make an excellent addition to any facility and provide safety and reliability.
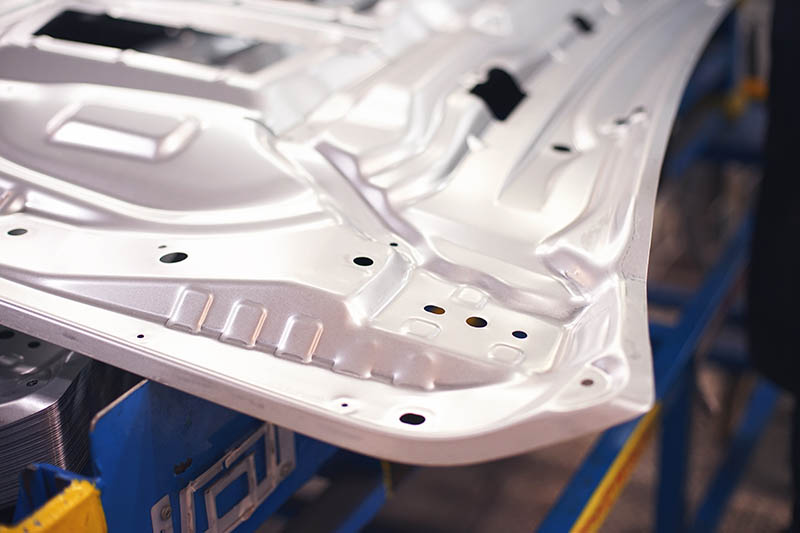
Benefits of Cold Isostatic Pressing
Cold Isostatic Pressing has become a widely used process for consolidation of metal, ceramic, plastic, and composite powders. Wet bag CIP is performed in rubber molds which can be manufactured to intricate shapes and various sizes. This creates uniform density throughout the green body resulting in predictable shrinkage during subsequent sintering or Hot Isostatic Pressing.
CIP can form parts too complex for uniaxial die presses. Cold Isostatic Pressed green bodies may also be machined quite easily prior to firing. Wet bag presses are capable of processing different size molds, multiple bags simultaneously, and very large parts. Most materials compact in the range between 10,000 to 40,000 psi. A research system with 60,000 psi capability allows testing to be done prior to scale up.
Achieve uniform density and strength
High Green Strength
Corrosion resistance
Decrease scrap loss and reduce mechanical scatter
Speak with a Specialist
Contact our team to get answers from highly trained industry professionals!
AIP3-12-60C RESEARCH CIP
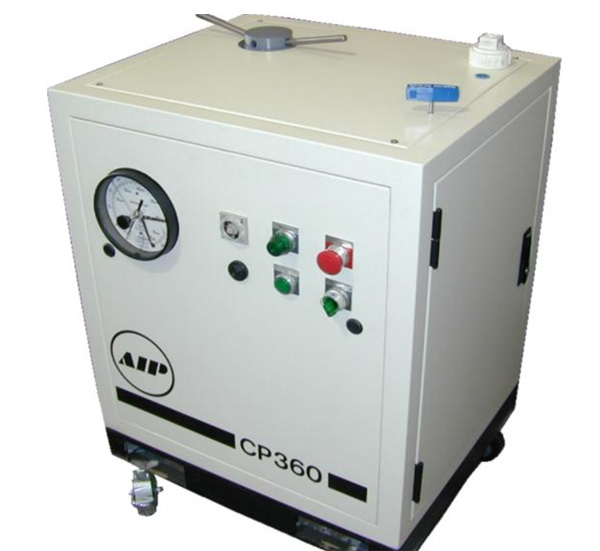
Research CIP System – Threaded
AIP3-12-60C RESEARCH CIP features customizable vessels with pressures up to 150,000 psi and sizes ranging from 2 to 60 inches in diameter. They offer various closure styles, pump options, and control systems, with optional warm pressing up to 100°C, ensuring versatility, safety, and efficiency for diverse applications.
AIP3-12-60CP RESEARCH CIP
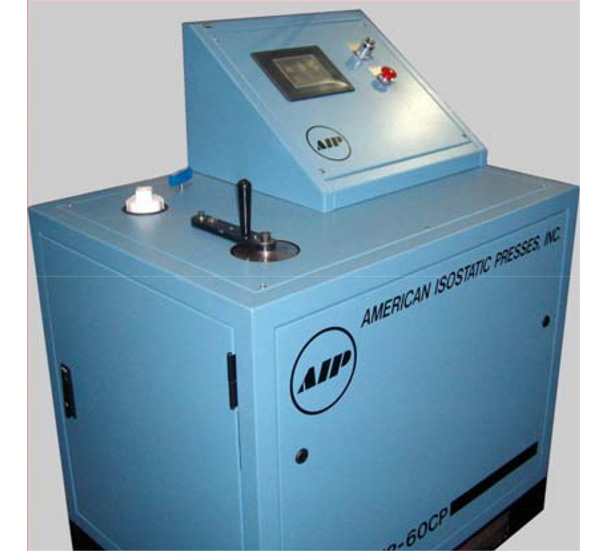
Research CIP Systems– Pin Type
The AIP3-12-60CP is a robust, customizable Cold Isostatic Press with a 60,000 psi capacity, featuring a 3" x 12" forged 4340 vessel, automated controls, and a Haskel pump. It's versatile, safe, and efficient, ideal for various applications, with optional warm pressing capabilities.
COLD ISOSTATIC PRESS SYSTEMS
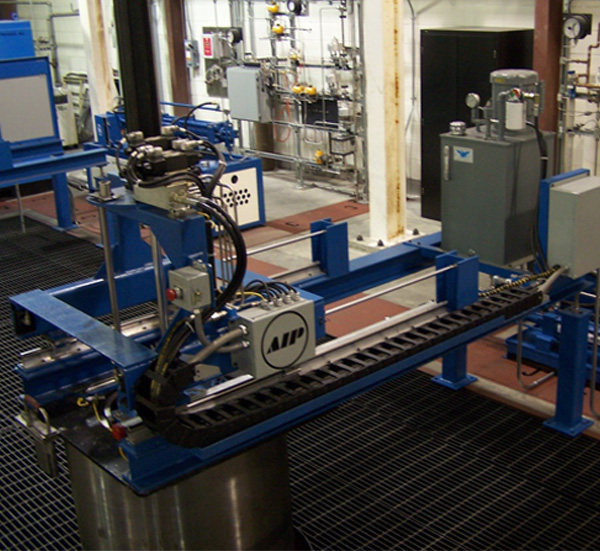
PRODUCTION COLD ISOSTATIC PRESS SYSTEMS
AIP's Production Cold Isostatic Press Systems offer a variety of sizes (12" to 30" diameter, up to 96" length) with a standard pressure of 30,000 psi. These systems, customizable in size and pressure, feature durable ASME Code vessel designs, suitable for different production needs.
Speak with a Specialist
Contact our team to get answers from highly trained industry professionals!
Why American Isostatic Presses?
Expertise
Over 30 years of knowledge and experience guides our work.
Integrity
Privately held with longstanding client relationships in all sectors.
Quality
Award-winning and board certified craftsmanship you can trust.
Our Superior Press Technology is Worldwide
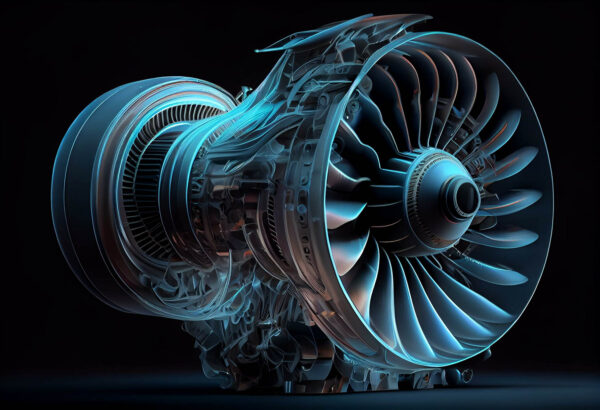
Aerospace
Advanced isostatic presses ensure aerospace components meet rigorous standards of strength and precision.
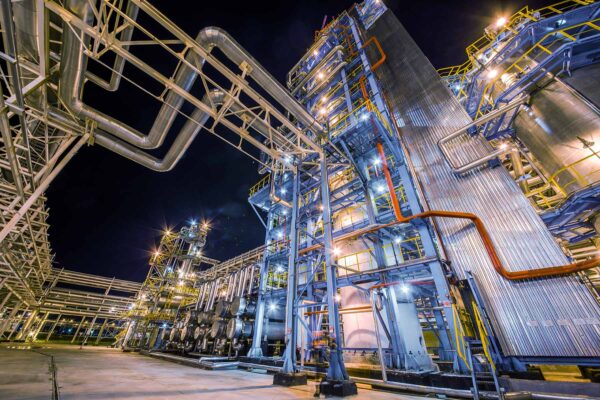
Energy
Efficient, high-quality component manufacturing for the energy industry is supported by specialized presses.
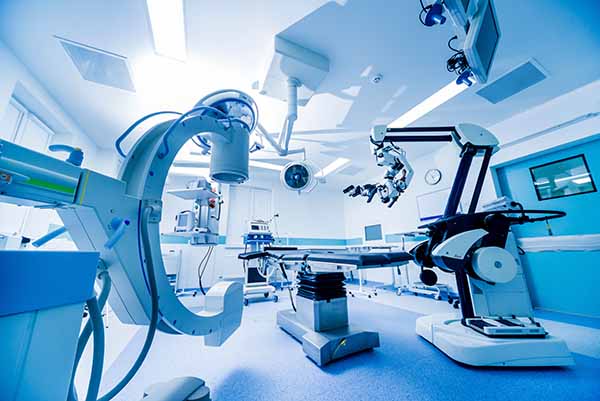
Medical
Isostatic presses enhance the development of medical devices, ensuring durability and precision.
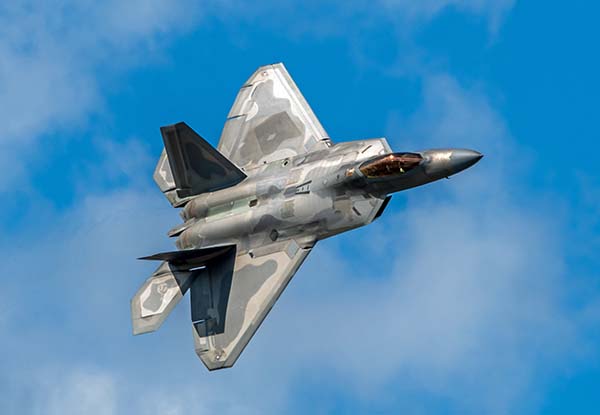
Defense
Robust isostatic presses are essential for producing high-standard, reliable components for defense.
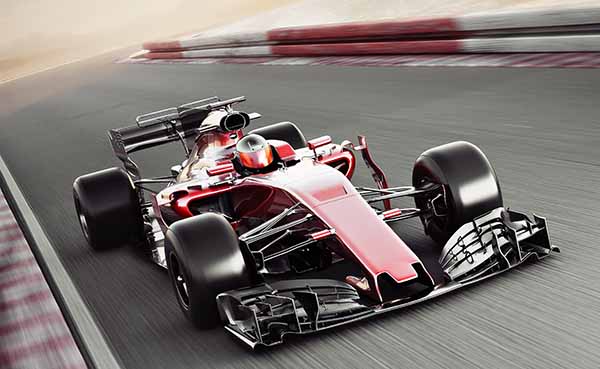
Automotive
Automotive manufacturing benefits from presses that enhance component durability and accuracy.
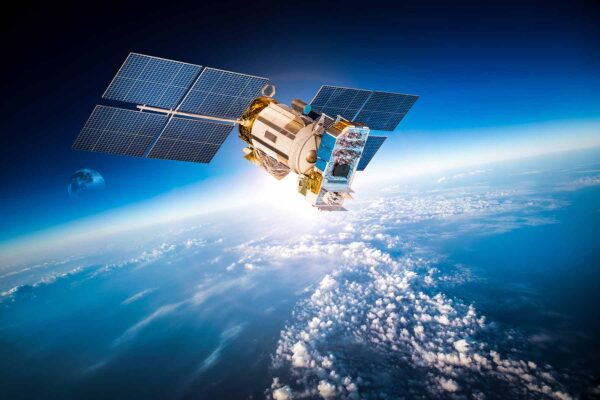
Space
Specialized presses support space exploration by providing components that withstand extreme conditions.